Additive manufacturing is a revolutionary technology that enables the creation of complex geometries and customized parts. However, metal additive parts have some limitations, such as poor surface finish, sharp edges and low mechanical properties. To overcome these challenges, hybrid additive manufacturing has emerged as a promising solution that combines metal additive manufacturing with conventional subtractive machining processes within a combined setup, where the advantages of each discrete process can be exploited synergistically.
How Does Hybrid Additive Manufacturing Work?
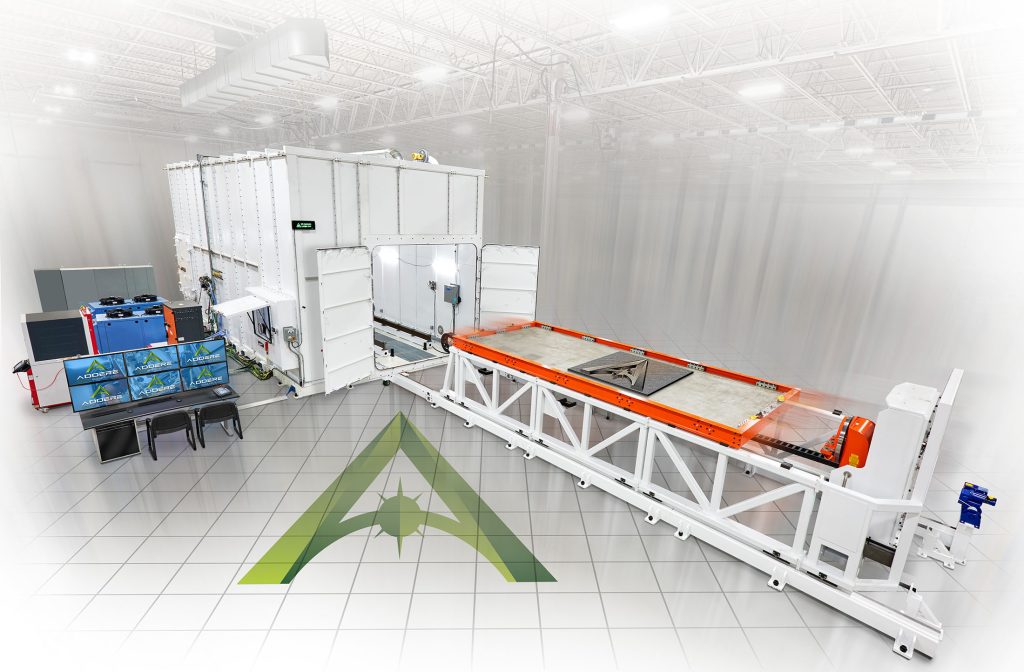
Hybrid metal additive manufacturing can be applied in different ways. The most common method is to use hybrid manufacturing to create a large-scale near-net shape metal alloy part that replaces a conventional casting or forging, followed by machining to finish the part to the required specifications. This way, the hybrid manufacturing process can reduce material waste, production time and cost, while improving the performance and functionality of the part.
Another method is to alternate between additive and machining in-process, creating features that are impossible or difficult to achieve with either process alone. For example, hybrid manufacturing can enable the creation of internal features by machining them as they are printed. Alternatively, hybrid manufacturing can enable the application of dissimilar metals to the same part by switching between the additive and subtractive processes.
What are the Benefits of Hybrid Additive Manufacturing
Hybrid manufacturing offers many benefits over conventional or standalone additive in areas such as:
- Enhanced surface quality and dimensional accuracy: Machining can improve the roughness and tolerance of the 3D printed parts, which can affect the performance and aesthetics of the final product.
- Improved mechanical properties: Machining can remove defects and residual stresses that are inherent in all 3D printed metal parts, which can improve the strength, fatigue and wear resistance of the material.
- Increased design freedom and functionality: Hybrid manufacturing can enable the creation of complex and customized geometries that are not feasible or economical with conventional or standalone additive, such as internal features, lattice structures or multi-material parts.
- Reduced material waste and energy consumption: Hybrid manufacturing can reduce the amount of material and energy required to produce a part, compared to conventional manufacturing, by minimizing the need for support structures, post-processing or multiple setups.
What are some Applications of Hybrid Manufacturing
Hybrid additive manufacturing is instrumental in applications, such as:
- Aerospace Components: Hybrid manufacturing can create lightweight yet robust aerospace components by combining additive processes for intricate structures and subtractive processes for critical surfaces.
- Automotive Prototyping: Hybrid manufacturing is valuable in the automotive sector for rapid prototyping, allowing for quick iterations of designs by combining additive processes for complex shapes and subtractive processes for fine-tuning.
- Petrochemical fixtures: Hybrid manufacturing can be utilized to manufacture unique one-off parts on demand from superalloy materials such as Inconel and titanium.
What are the Challenges of Hybrid Manufacturing
Despite the some of challenges hybrid manufacturing presents, ADDere has solutions that will make this process successful, such as:
- Process integration and optimization: Hybrid manufacturing requires a high level of coordination and synchronization between the additive and subtractive processes, which can pose technical and operational difficulties. ADDere has solved this with software that carefully optimizes the process parameters, such as feed rate, laser power and tool path, to ensure the quality and efficiency of the part.
- Process modeling and simulation: Hybrid manufacturing involves complex physical phenomena, such as thermal, mechanical, and metallurgical interactions, that affect the behavior and outcome of the process. ADDere provides advanced modeling and simulation tools that can accurately predict and control the process performance and the part properties.
- Process monitoring and control: Hybrid manufacturing involves dynamic conditions, such as temperature, distortion or defects, that can affect the reliability and repeatability of the process. ADDere has real-time monitoring and feedback systems to detect and correct any deviations or errors during the process.
Hybrid manufacturing is a proven technology that can enhance the capabilities and performance of additive manufacturing by combining it with subtractive processes. ADDere’s hybrid manufacturing processes can offer many benefits to a wide berth of industries, such as improved surface quality, mechanical properties, design freedom and material efficiency while overcoming some of the limitations of conventional or standalone additive manufacturing. Additive manufacturing is expected to play a key role in the future of manufacturing, as it can enable the creation of innovative and functional products that can meet the demands and challenges of the modern world.
In the dynamic world of manufacturing, innovation is the driving force behind efficiency, precision and cost-effectiveness, and ADDere is at the forefront of it. If you are looking to move your conventional manufacturing process to one that of additive manufacturing, then contact us today and speak with one of our additive experts. We can guide you through the process and provide our expert opinion on improving your manufacturing processes.