Titanium in the Aerospace Industry
Why Titanium is used in Aerospace
Titanium is one of the most durable and expensive metals in the world today. The rarity of the element and its high cost of production makes it an expensive metal, but despite the high price tags, the aircraft manufacturing industry is still looking for the material to build their products as it offers a spectacular strength-to-weight ratio and thermodynamic properties. Titanium-based alloys can become products that will be used to build a number of aerospace components used in engines, airframes and mechanical components.
More than a century after its first discovery, scientists found a fit in the commercial aerospace and defense industries. Since then, many firms are using the element to produce alloys that will be used to create a variety of aircraft components. Engineers point to the materials’ higher weight-to-strength ratio than steel and aluminum, Titanium’s performance when exposed to high temperatures, and the material’s ability to resist corrosion making it a valuable metal for making airplanes.
Where Titanium is used in Aerospace
The aerospace industry is also spending large budgets on developing manufacturing processes that try to make the building of titanium components more cost-effective. While today’s methods of either casting or machining titanium alloys from billet are what’s considered most effective, new technologies like laser wire additive manufacturing found in the ADDere process can reduce production costs and development time by printing titanium alloys at scale and reduce costly titanium machining time. As production prices come down, the unique characteristics of the material become more and more tantalizing.
Fuel is a limited resource and aircraft consume a lot of it when they fly. To help reduce the energy costs of flight, many aircraft manufacturers are resorting to using Titanium to build fuel-efficient airplanes. The weight-to-strength ratio of Titanium makes it the best material of choice when building an airplane’s turbine engine power plants, airframe structural elements and other mechanical elements. Titanium alloys are lighter than other metals, and it also has greater durability.
Titanium is able to resist high temperatures and corrosion, especially when it makes contact with CFRPs, also known as carbon fiber-reinforced polymers. When the airplane takes off or lands, the friction that it creates when reaching for the runway is what generates extreme heat. Using Titanium, the damages incurred from these events can be lowered. Engine components, landing gear, and airframes of aircraft are now manufactured more and more out of Titanium. Airline companies are increasing the use of these advanced materials as they are more reliable compared to other metals.
Aside from the aircraft components and airframes, Titanium is also used to build modern turbine engines. Many aircraft manufacturers have implemented the use of Titanium in creating engines due to their low weight and higher strength. Airplanes that use engines that are made from Titanium have better flight performance compared to other airplanes that are made from other metal alloys. Titanium alloys can also withstand extreme temperatures found in today’s high-efficiency turbine power plants. This material characteristic is pushing more airplane manufacturers to expand their use of Titanium, and discover where it can be applied further.
ADDere’s additive manufacturing can streamline the development and production process of large-scale components made from titanium. Contact us today and see if your manufacturing operations can benefit from ADDere’s additive manufacturing with titanium.
do you want to learn more about ADDere's products and services?
What's going on at ADDere
Latest Blog Posts
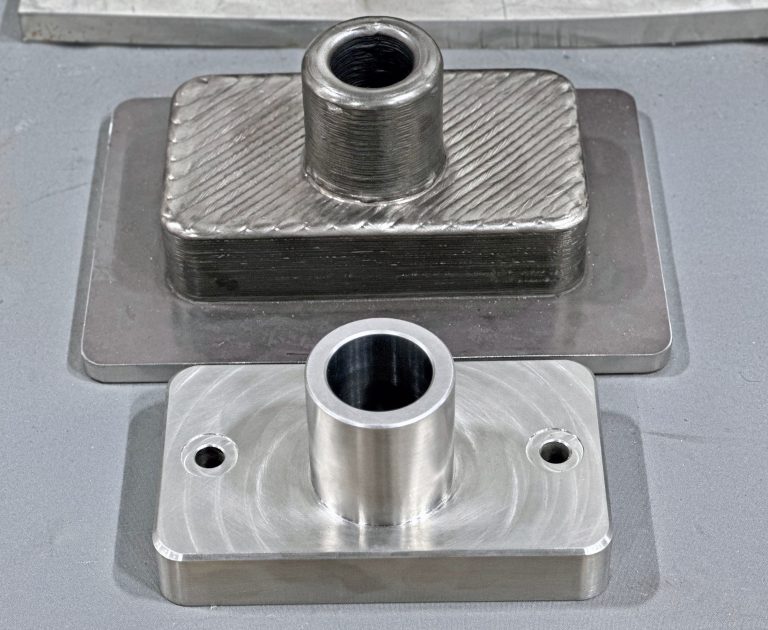
Are 3D Printed Metal Parts Produced with ADDere Strong?
ADDere’s additive manufacturing has revolutionized the production of strong metal-alloy parts, offering unprecedented flexibility and precision. One of the most exciting developments in this field
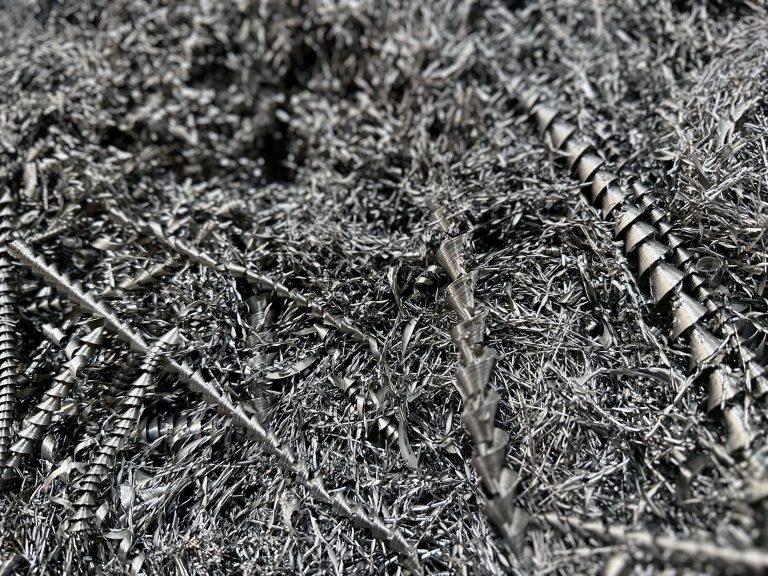
Mitigate Tariffs on Steel by Reshoring Your Manufacturing with ADDere
When it comes to large-scale metal parts manufacturing, ADDere can be a lifesaver for many businesses concerned with high import prices of steel. For decades,
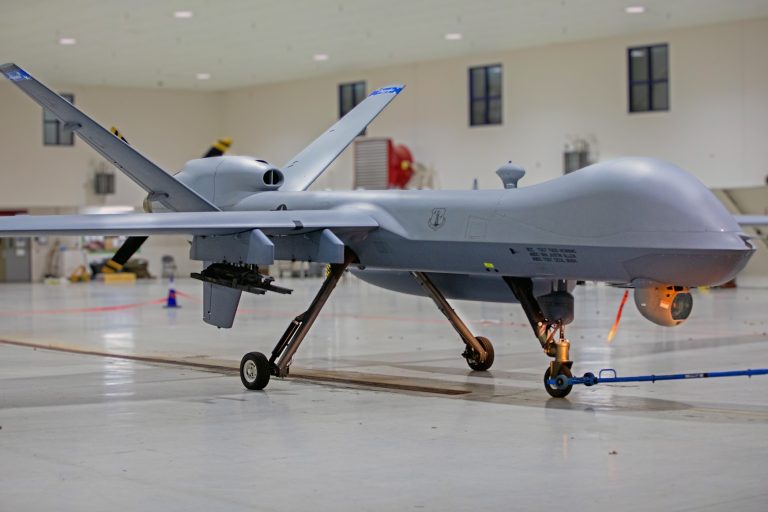
Harnessing ADDere’s Additive Manufacturing Process for Next-Generation Drones
Industrial applications of drones are soaring to new heights in 2025. From utilities and infrastructure inspection to agriculture and defense applications are industries that will
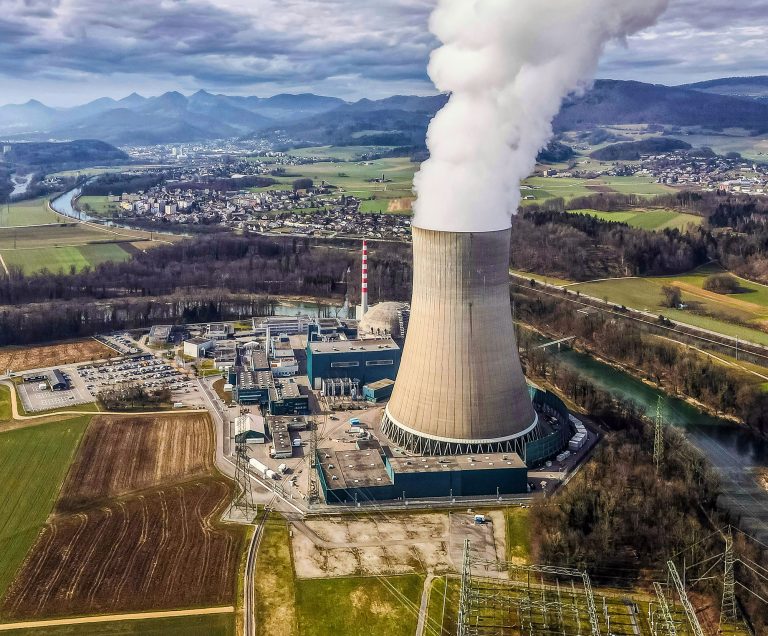
From Concept to Core: How ADDere Transforms Nuclear Reactor Components
Additive manufacturing has been gaining traction in the nuclear energy industry. The development and maintenance of nuclear reactors demand components that meet stringent safety standards
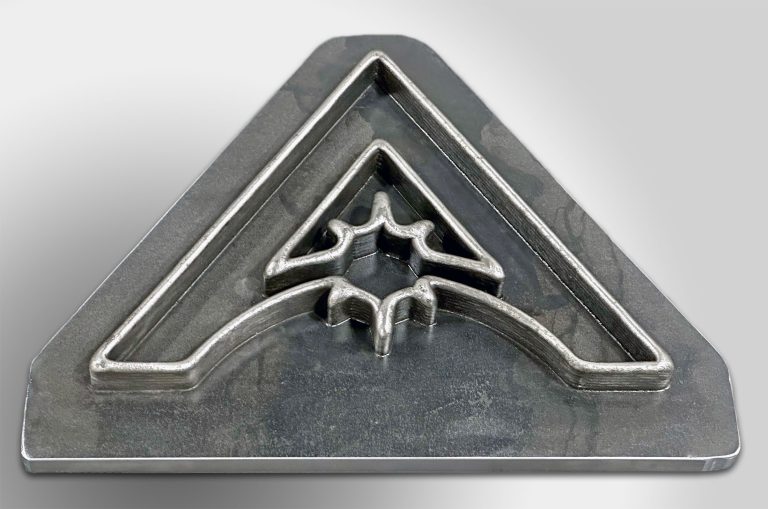
White Paper: The Impact of Additive Manufacturing on Cost, Efficiency & the Future
ADDere’s metal laser-wire additive process is a proven technology for producing complex large-scale metal parts for the defense and aerospace industries. With increasing interest in
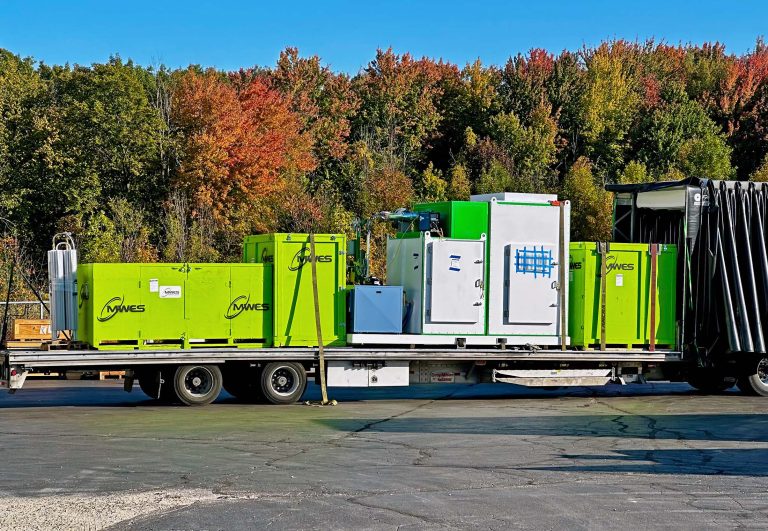
Cost-Benefit Analysis of ADDere’s Additive Manufacturing Process
ADDere’s metal additive manufacturing process has transformed the manufacturing landscape by enabling the production of complex parts with unprecedented precision. Additive manufacturing has evolved from