Titanium in the Automotive Industry
Why use Titanium in the automotive industry
With Titanium’s high melting point, corrosion resistance, and lightweight, it is becoming a highly desirable metal in the automotive industry. Utilizing titanium will result in lighter automotive parts that retain the same strength and integrity as the original steel parts. This in turn can improve the vehicle’s fuel economy and reduce its carbon footprint.
Luxury auto manufacturers, such as Bugatti, have begun using titanium in parts throughout the vehicle that continuously faces high-heat and corrosive environments. Brake calipers, engine valves, tire rims, and other mechanical parts are some of the many components that have been made from titanium. Titanium has the added benefit of continued strength versus traditional steel parts with also a reduction in the parts’ overall weight. This reduction in weight can help improve fuel and energy efficiency, and also the carbon emissions from the vehicle as a whole. Titanium is also known for being highly corrosion resistant, something that all automobiles face from elements like road salt and extreme cold. Parts made from Titanium will ultimately extend the life of the individual part and the vehicle as a whole.
Currently, the only limiting factor to the widespread use of titanium in the construction of automobiles is its relatively high cost of production, at roughly $4,800 USD per metric ton in 2018. In the future, improvements to the production and procurement of titanium should bring the cost of the metal down to the point where it can be priced competitively with steel.
As the manufacturing process of titanium improves and the costs come down, there will be a lucrative future for this metal in the construction of consumer-grade vehicles. Titanium one day could be as commonplace as aluminum or steel in our cars or motorcycles.
ADDere’s additive manufacturing can streamline the development and production process of large-scale components made from titanium. Contact us today and see if your manufacturing operations can benefit from ADDere’s additive manufacturing with titanium.
do you want to learn more about ADDere's products and services?
What's going on at ADDere
Latest Blog Posts
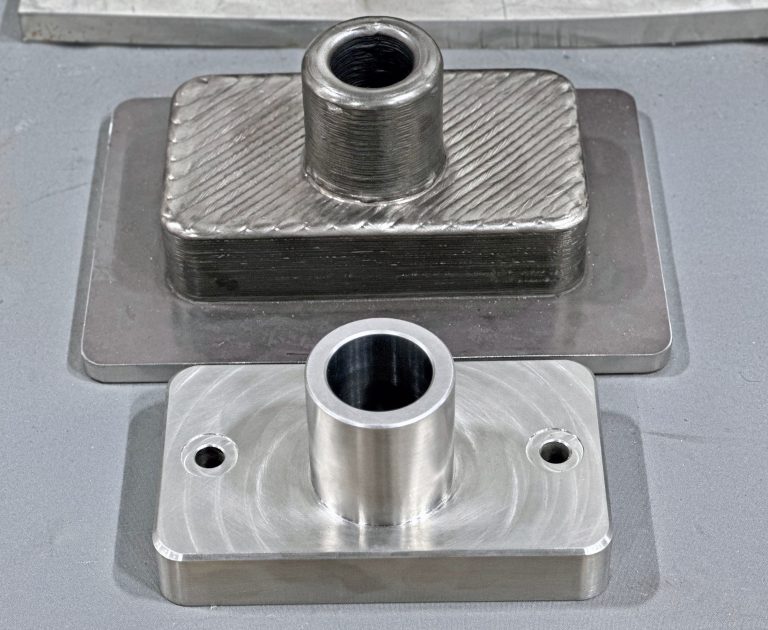
Are 3D Printed Metal Parts Produced with ADDere Strong?
ADDere’s additive manufacturing has revolutionized the production of strong metal-alloy parts, offering unprecedented flexibility and precision. One of the most exciting developments in this field
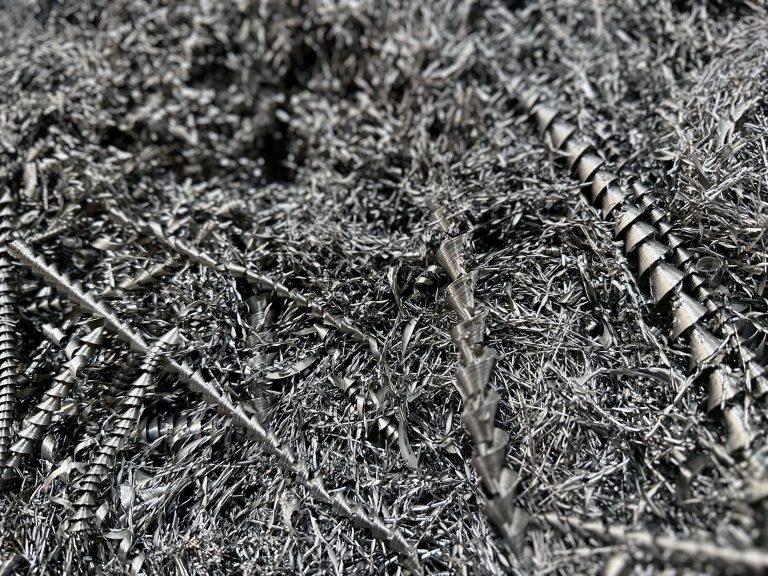
Mitigate Tariffs on Steel by Reshoring Your Manufacturing with ADDere
When it comes to large-scale metal parts manufacturing, ADDere can be a lifesaver for many businesses concerned with high import prices of steel. For decades,
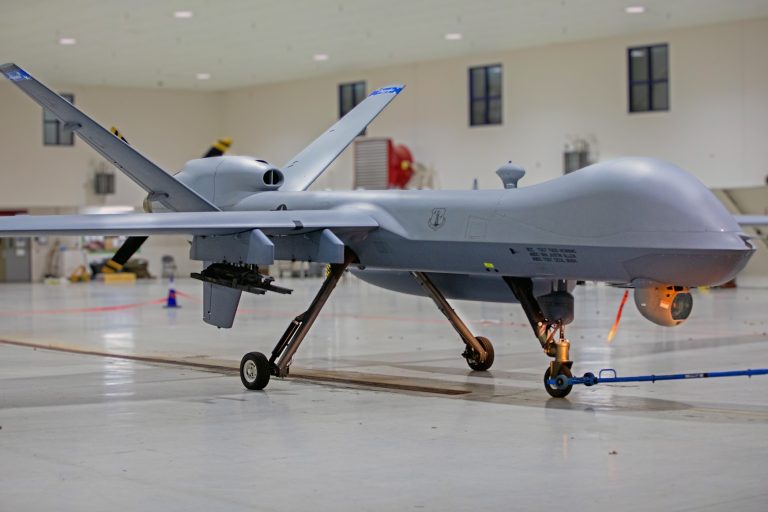
Harnessing ADDere’s Additive Manufacturing Process for Next-Generation Drones
Industrial applications of drones are soaring to new heights in 2025. From utilities and infrastructure inspection to agriculture and defense applications are industries that will
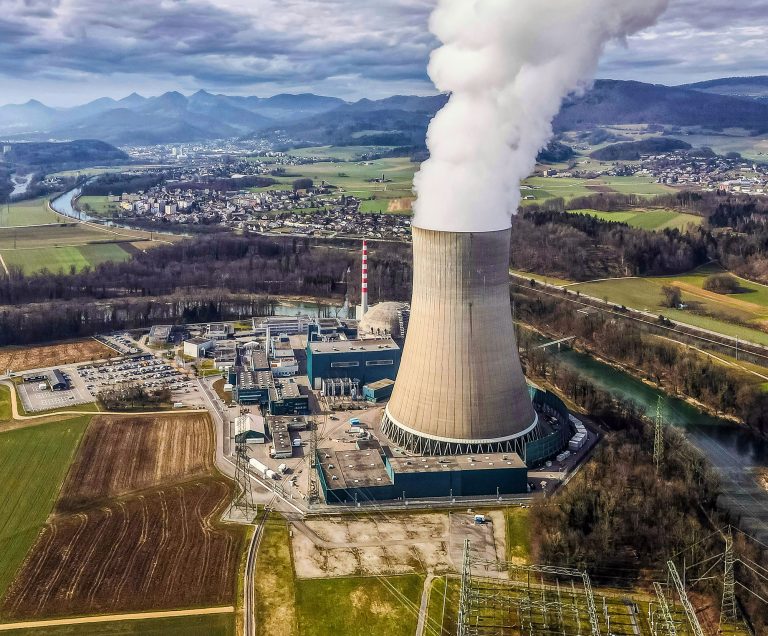
From Concept to Core: How ADDere Transforms Nuclear Reactor Components
Additive manufacturing has been gaining traction in the nuclear energy industry. The development and maintenance of nuclear reactors demand components that meet stringent safety standards
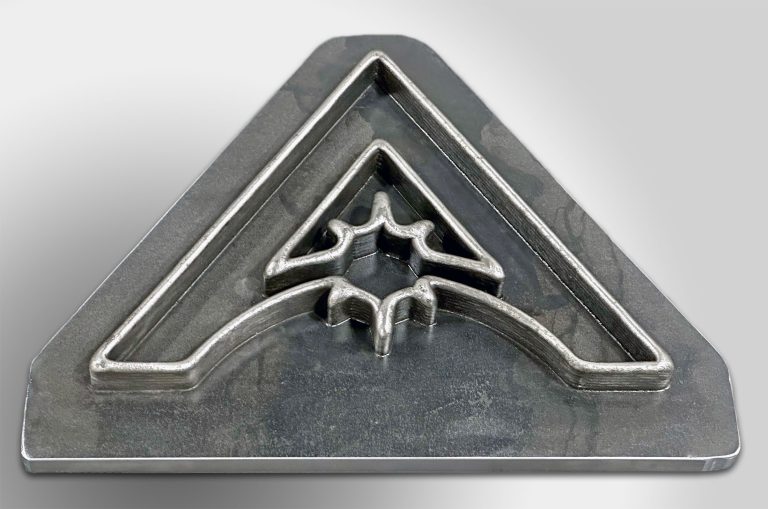
White Paper: The Impact of Additive Manufacturing on Cost, Efficiency & the Future
ADDere’s metal laser-wire additive process is a proven technology for producing complex large-scale metal parts for the defense and aerospace industries. With increasing interest in
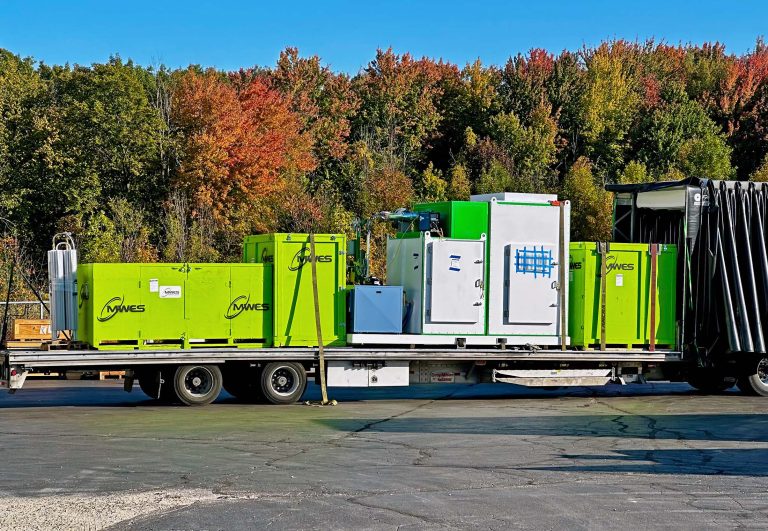
Cost-Benefit Analysis of ADDere’s Additive Manufacturing Process
ADDere’s metal additive manufacturing process has transformed the manufacturing landscape by enabling the production of complex parts with unprecedented precision. Additive manufacturing has evolved from