Titanium in the Defense Industry
How the defense industry uses titanium
Titanium has become an increasingly popular material to use across the military and defense industry, with the material offering a substantial number of benefits across the majority of vehicles and structures both areas use. The metal’s popularity began in the early 1960s and has continued to grow since then, as it’s a lightweight material that offers much more durability per weight than the likes of steel and other manufacturing materials. With the advent of additive manufacturing with metals, its utility will only grow.
Where Titanium Used in the Defense Industry
Over the past few decades, the material has been used in a variety of different applications across the military and defense spectrum. Depending on which arm of the defense it’s being used in, however, it offers a variety of different uses, thanks in large part to the versatility and adaptability that it provides when being shaped and manufactured.
Aircraft Manufacturing with Titanium
Titanium has been used in a variety of aircraft applications over the past few decades, thanks in large part to its strength-to-weight ratio, which is considerably more beneficial than many other materials. This advantage offers a significant amount of strength while minimizing the overall weight of an aircraft, with this durability being seen in the majority of environmental conditions.
The material has also been shown to offer considerable performance when transitioning from one temperature to another at high speeds. This quality has allowed it to be used on a number of military aircraft with much of the applications being in their exteriors and engines, although it’s also used in a variety of other components, such as firewalls and landing gear. For the majority of these applications, however, titanium is typically integrated with the likes of aluminum to achieve optimal performance.
The ease of manufacturing and shaping the material using metal 3D printing capabilities like the ADDere laser wire additive manufacturing process means that titanium can be used for more accurate, and effective, ballistic protection for most of an aircraft’s critical parts. It’s also been noted that, as titanium is lightweight and provides a significant amount of structural integrity per pound, it can be a much more weight-effective option than many other materials for aircraft.
Its material properties have led to titanium being used in a number of aircraft types, with one of the most notable being the Lockheed SR-71 Blackbird, 93% of which weight consists of alloys that feature the material. The metal is also used in a few other notable aircraft, such as the Lockheed Martin F-22 Raptor, of which 42% of its weight is made up of alloys that contain titanium and the Lockheed Martin F-35 Lightning II, where titanium accounts for around a third of the aircraft’s weight.
The majority of titanium that’s imported into the United States is used in the aerospace niche with 72% of the material being used in the sector. The rest of the imports go toward the likes of chemical processing, the medical sector and much more. As such, the importance of the material in the niche can’t be understated, with the majority of this being driven by its high-performance levels achieved under a significant amount of heat.
Outside of defense, the material is used in a variety of commercial aircraft, with much of this being seen in the Airbus A350 and A380 commercial airliners. The metal can withstand temperatures of up to 1112°F (600°C), which has made it a much more practical choice when it comes to manufacturing jet engines and other areas that are regularly put into contact with a considerable amount of heat.
Naval Uses of Titanium
Titanium has also been increasingly popular in the naval sector, with interest originally being driven by its popularity in commercial ships. This is primarily because salt water has almost no effect on the material. The property is a considerable advantage when compared to the majority of other metals, as it avoids corrosion, lowering the need for regular maintenance because of the negative effects of saltwater.
The lack of corrosion from sea water has meant that titanium has become increasingly popular in the exterior of many submarines and other naval vessels, with the material being used in the likes of exhaust stack liners, submarine ball valves, fire pumps and heat exchangers, as well as the majority of a submarine’s piping and cooling systems.
Before titanium made its way throughout the navy, the primary material used in heat exchangers was a copper-nickel blend, which needed to be maintained and replaced regularly. Since being replaced, this has meant that the lifespan of various submarine components has been drastically improved, which has improved cost-efficiency across the navy.
Different Grades of Titanium and Their Uses
There are three different grades of titanium. The differing properties of these grades can have quite a significant impact on how it’s used. The first of these is 6AL-4V ELI, which is best known for its ability to withstand a large amount of heat and has primarily been used in the like of aircraft turbines and jet engines. 6Al-6V-2Sn Ti, on the other hand, is typically seen in the likes of landing gear, airframes, ordnance components, and rocket cases. Lastly is Grade 5, which is the more common alloy seen across the aerospace niche, as it’s specifically treated to increase its strength and withstand a drastically high-temperature level.
Why Titanium Became Popular in the Defense industry
Because of how popular the material has been in the area for the past several decades, many people may believe that it’s always been used in the niche. However, this hasn’t always been the case, and it was only in the late 1940s that the United States government began implementing it across a variety of different sectors. This is chiefly because of the benefits that many commercial airlines, as well as a variety of foreign governments, began seeing with the metal, especially when blended with a few other materials.
This increase in use was quite rapid; in 1947, the United States manufactured two tons of the material, and by 1953, this had grown to over two million pounds. Since then, it’s been increasingly used in a variety of different areas, both in defense and in commercial products, as well as in medicine and a variety of other sectors.
One of the hurdles that stand in the way of greater titanium adoption is the difficulty of machining the metal. As can be imagined with such a tough material, it takes specialized cutting tools and processes to form the metal from the billet. Machining is usually preferred as the costs of casting titanium parts can be higher due to the high melt temperatures of the materials requiring specialized furnaces to perform.
With the arrival of 3D metal printing, the forming of titanium has gotten much easier where small-scale parts could be easily printed with selective laser sintering additive processes and larger structures can more economically be made with Laser wire additive manufacturing systems. The former can create massive near-net-shaped parts out of titanium, drastically reducing the machining and fabrication times of large titanium parts and greatly reducing scrap rates.
ADDere’s additive manufacturing can streamline the development and production process of large-scale components made from titanium. Contact us today and see if your manufacturing operations can benefit from ADDere’s additive manufacturing with titanium.
do you want to learn more about ADDere's products and services?
What's going on at ADDere
Latest Blog Posts
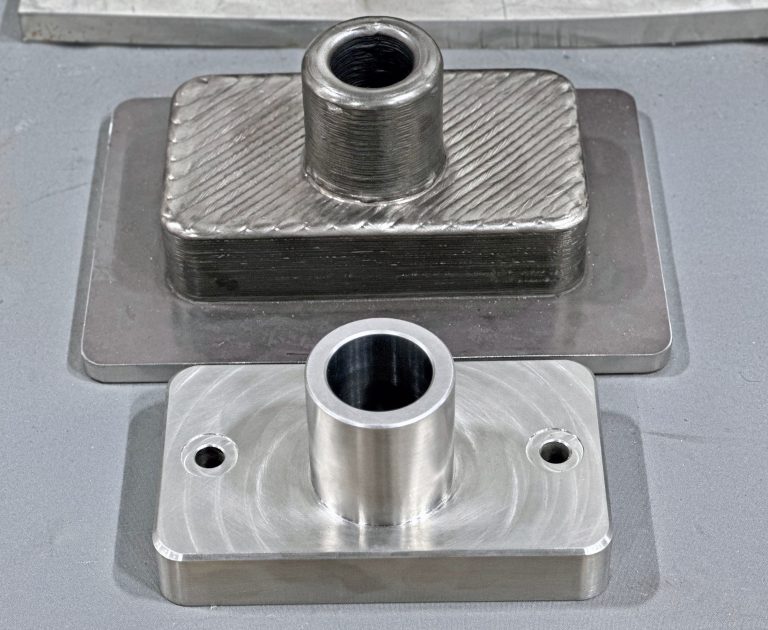
Are 3D Printed Metal Parts Produced with ADDere Strong?
ADDere’s additive manufacturing has revolutionized the production of strong metal-alloy parts, offering unprecedented flexibility and precision. One of the most exciting developments in this field
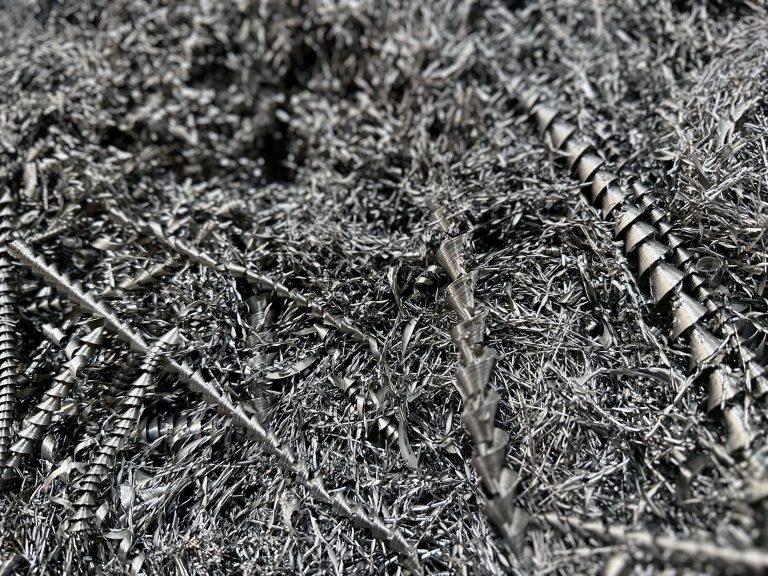
Mitigate Tariffs on Steel by Reshoring Your Manufacturing with ADDere
When it comes to large-scale metal parts manufacturing, ADDere can be a lifesaver for many businesses concerned with high import prices of steel. For decades,
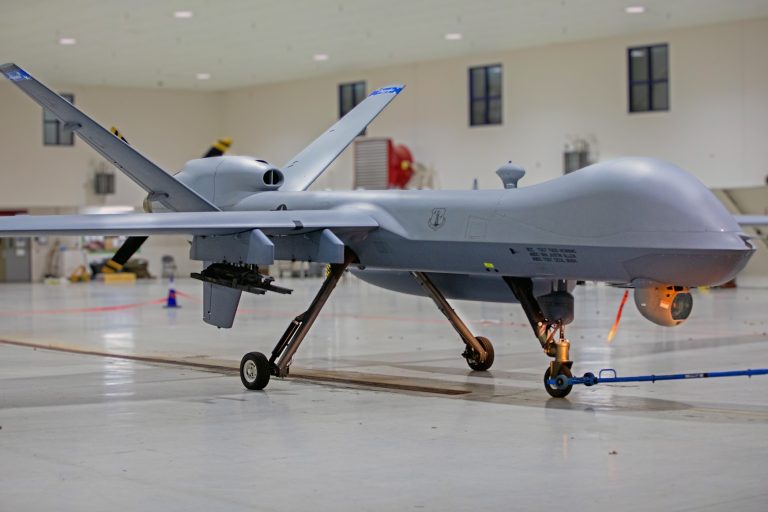
Harnessing ADDere’s Additive Manufacturing Process for Next-Generation Drones
Industrial applications of drones are soaring to new heights in 2025. From utilities and infrastructure inspection to agriculture and defense applications are industries that will
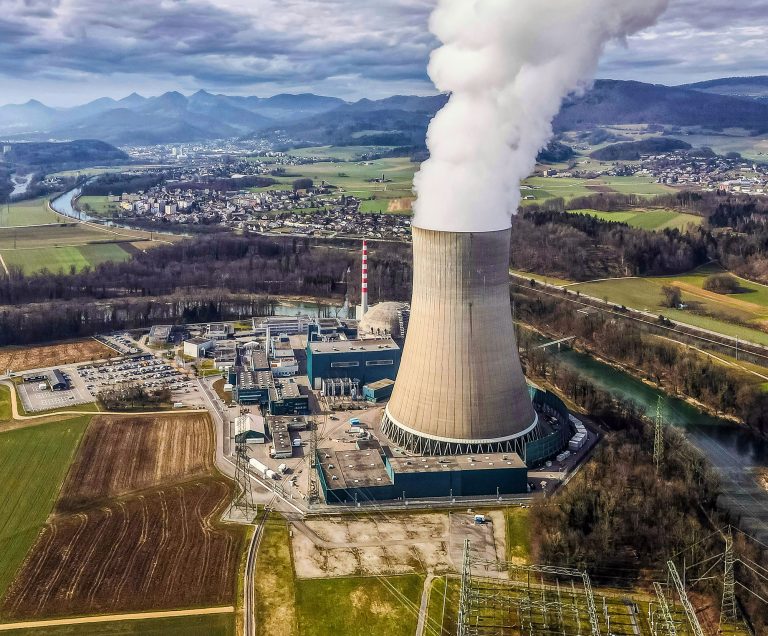
From Concept to Core: How ADDere Transforms Nuclear Reactor Components
Additive manufacturing has been gaining traction in the nuclear energy industry. The development and maintenance of nuclear reactors demand components that meet stringent safety standards
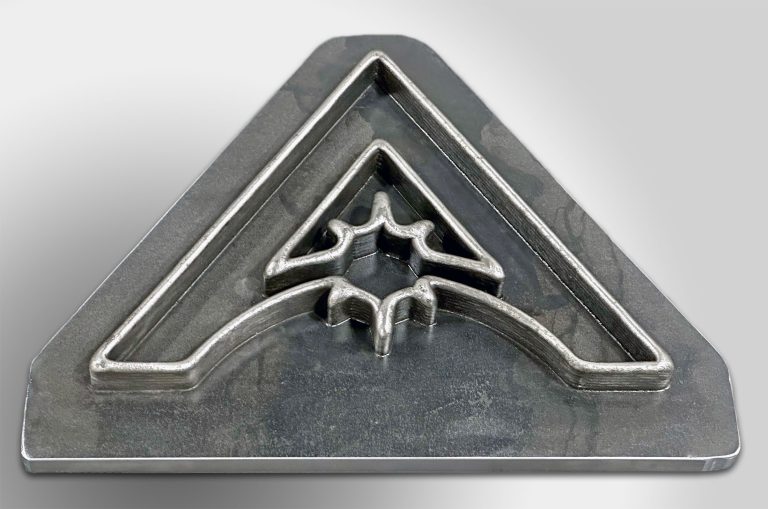
White Paper: The Impact of Additive Manufacturing on Cost, Efficiency & the Future
ADDere’s metal laser-wire additive process is a proven technology for producing complex large-scale metal parts for the defense and aerospace industries. With increasing interest in
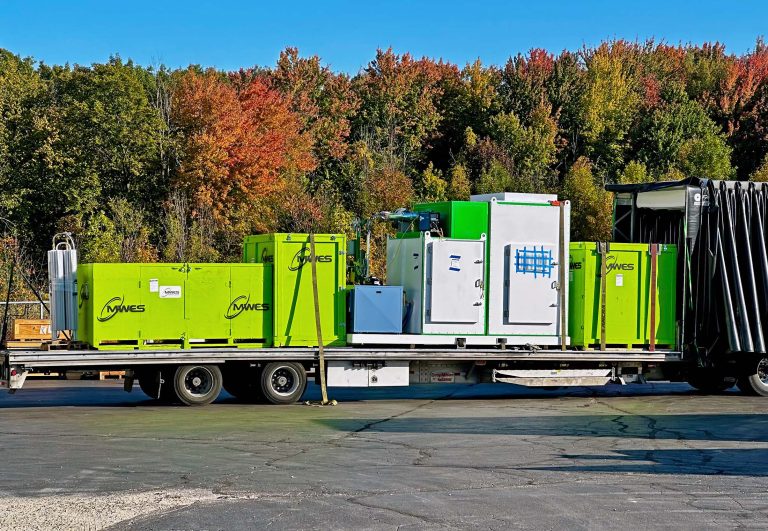
Cost-Benefit Analysis of ADDere’s Additive Manufacturing Process
ADDere’s metal additive manufacturing process has transformed the manufacturing landscape by enabling the production of complex parts with unprecedented precision. Additive manufacturing has evolved from