Petrochemical Industry
Additive Manufacturing is right at home in the Petrochemical Industry
In the Oil & Gas industry, where one-off unique parts are quite common, the ADDere laser-wire additive manufacturing system can produce parts directly from a CAD model into a casting-level part ready for final machining without the need to produce molds. Typically parts have to be cast from molds, which can be a time-consuming and costly endeavor for just a one-off part. But with additive manufacturing, components can be built on demand from fewer interlocking parts making them less prone to failure.
The ADDere large-scale metal 3D printing system allows components to be manufactured in-house and made from more exotic superalloys. Components made from such alloys are far more resistant to harsh chemicals and environments and have the added benefit of being 3D printed on location.
Petrochemicals Meet Superalloys
Petrochemicals from the refinement process of petroleum and natural gas can be hazardous. The highly acidic petrochemicals can potentially eat through the traditional steel storage vessels or piping. These highly corrosive chemicals require extra care in their production, transportation and storage. Storing highly toxic and corrosive chemicals has to be done with great care, such that even a small leak can lead to long-term environmental damage. Not only that, during the refinement process, temperatures can reach highs at over 1,000°F (538°C), and at those temperatures, the steel begins to lose much of its tensile strength causing cracks to form.
The solution to improving tensile strength has been substituting nickel-based superalloys in place of steel. These alloys are far more resistant to high temperatures, oxidation and corrosion than traditional steel. Petrochemicals generally have highly toxic and acidic properties making superalloys more in demand than ever to store and transport such acidic chemicals. Superalloys even hold up better than steel in high-stress environments under most circumstances. Nickel-based superalloys typically contain alloying elements such as chromium, aluminum, titanium, molybdenum, tungsten, niobium, tantalum and cobalt. From a combination of those alloying elements, superalloys are formed, like Hastelloy, Inconel, Monel and Incoloy to name a few.
Superalloys can be fabricated into a wide range of components large or small, from pipes, tubes, fittings, turbine blades, pumps and valves to even entire storage vessels. Any part that can be made from steel can also be made from superalloys. Components like these made from a superalloy have the tendency to be much stronger and more resistant to the corrosive and oxidation effects of petrochemicals.
Where ADDere comes in
With the increasing demand for utilizing superalloys in the construction of the facilities to manufacture, store and transport petrochemicals, the ADDere laser-wire additive manufacturing process is the ideal manufacturing process for the production of components made from superalloys.
From just a standard 3D CAD model, the ADDere manufacturing process can quickly and cost-effectively produce accurate and clean parts on demand. The ADDere additive manufacturing system can be set up on-site to allow for faster part fit-up times than traditional part machining. This eliminates the need to source out builds from other vendors who traditionally produce parts from expensive castings.
The ADDere laser-wire metal additive manufacturing process has the capability to 3D print components in a wide range of widely used metals, including many superalloys. Parts made from superalloys tend to have more tensile strength and resistance to corrosion than the same part made from steel. Components made using ADDere’s additive manufacturing process will require minimal machining to finish a part with very little material waste.
The ADDere additive process can produce parts of any size commonly used in the Oil & Gas industry including piping, turbine blades, storage vessels and beyond. Traditionally, parts made from superalloys are difficult and expensive to machine making larger parts impractical to produce through machining. However, parts produced with the ADDere additive manufacturing process can be made to be quite large in scale. Additive manufacturing reduces the need to join many smaller interlocking parts together to create a single component, eliminating many failure points in the process.
With the costs and time associated with machining and welding superalloys, the ADDere additive manufacturing process produces exceptionally pure, high-quality metallurgy across the entire build. 3D printed components can utilize as much as 99% of the material used to make the part, with only a 1-2% material loss rate. Components this pure reduce the cost and material waste associated with the complexities of any further machining or welding that may be required to finish the part.
Typical Petrochemical components that ADDere can fabricate
Is ADDere right for you?
If your business is looking to manufacture components for the petrochemical industry from superalloys in a fast, cost-effective way, then contact us today. The ADDere large-scale laser-wire additive manufacturing process can print in sizes and materials to fit your business’s needs.
do you want to learn more about ADDere's products and services?
What's going on at ADDere
Latest Blog Posts
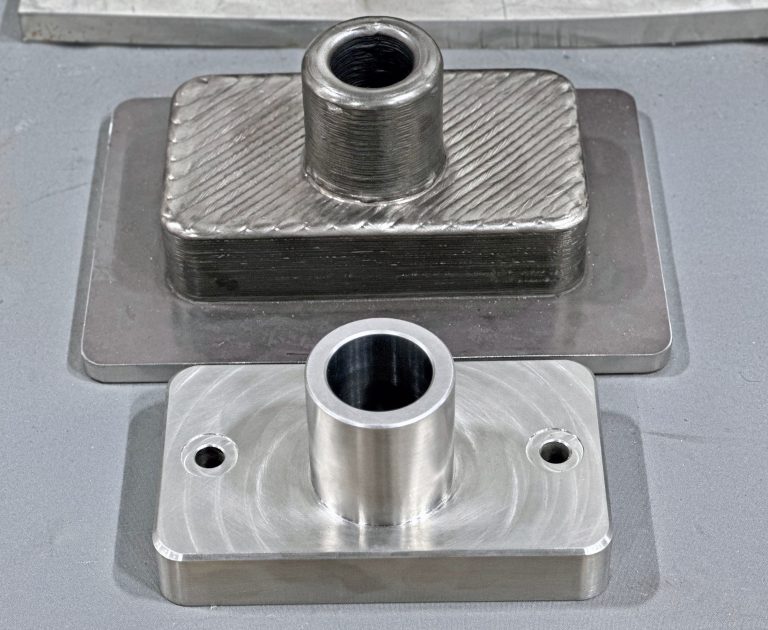
Are 3D Printed Metal Parts Produced with ADDere Strong?
ADDere’s additive manufacturing has revolutionized the production of strong metal-alloy parts, offering unprecedented flexibility and precision. One of the most exciting developments in this field
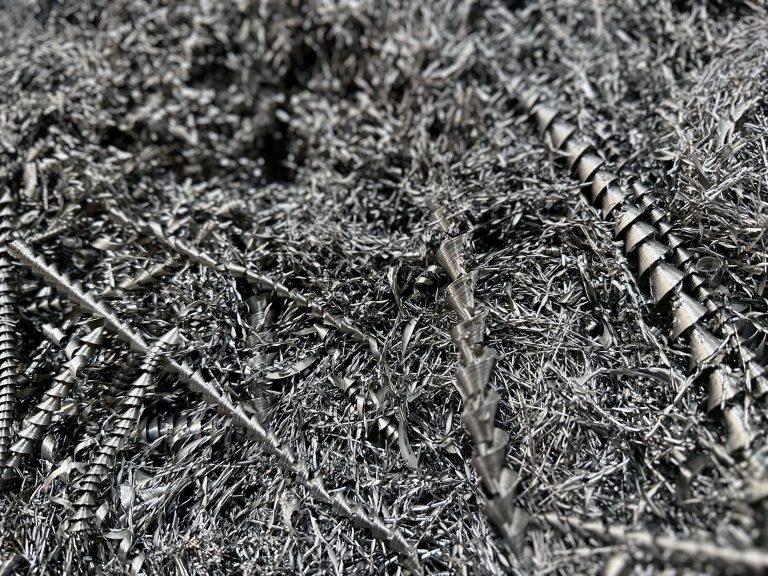
Mitigate Tariffs on Steel by Reshoring Your Manufacturing with ADDere
When it comes to large-scale metal parts manufacturing, ADDere can be a lifesaver for many businesses concerned with high import prices of steel. For decades,
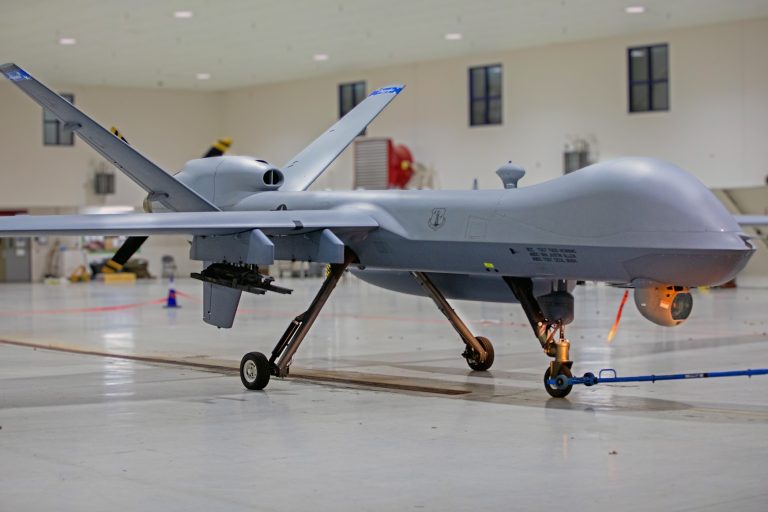
Harnessing ADDere’s Additive Manufacturing Process for Next-Generation Drones
Industrial applications of drones are soaring to new heights in 2025. From utilities and infrastructure inspection to agriculture and defense applications are industries that will
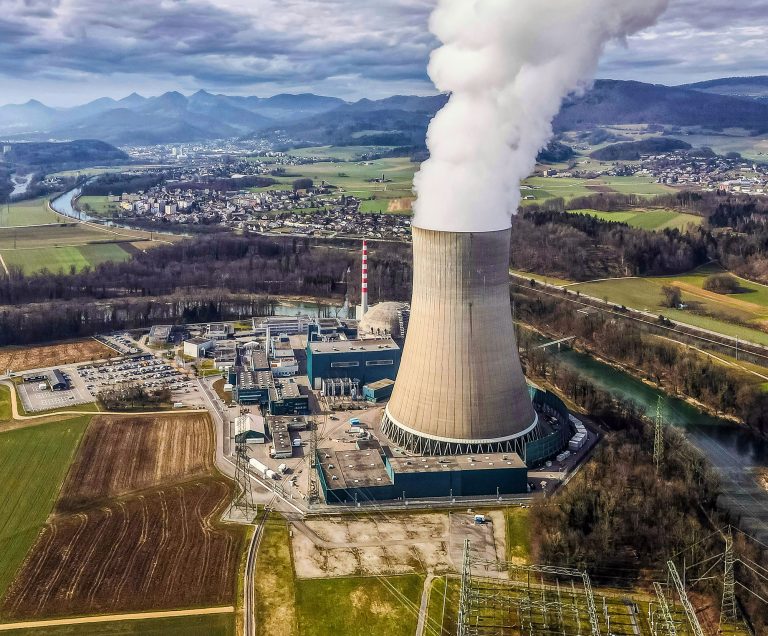
From Concept to Core: How ADDere Transforms Nuclear Reactor Components
Additive manufacturing has been gaining traction in the nuclear energy industry. The development and maintenance of nuclear reactors demand components that meet stringent safety standards
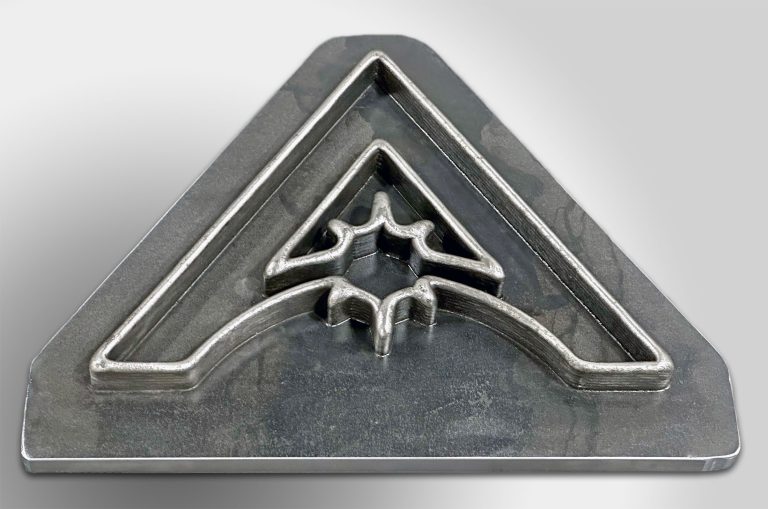
White Paper: The Impact of Additive Manufacturing on Cost, Efficiency & the Future
ADDere’s metal laser-wire additive process is a proven technology for producing complex large-scale metal parts for the defense and aerospace industries. With increasing interest in
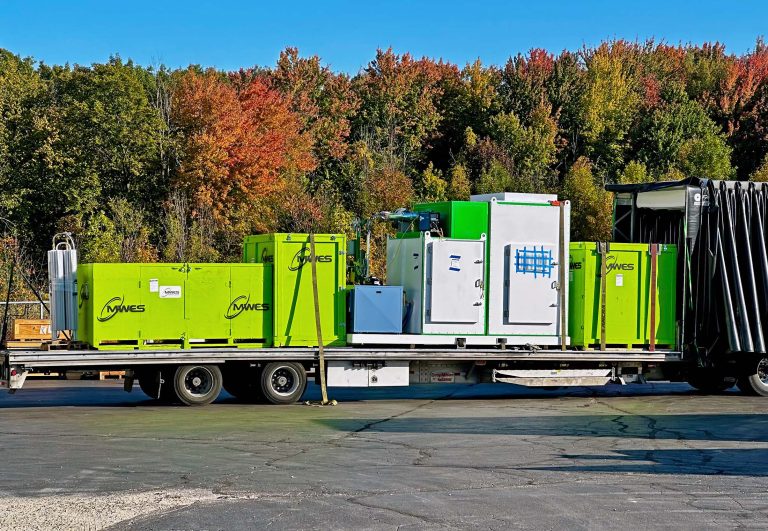
Cost-Benefit Analysis of ADDere’s Additive Manufacturing Process
ADDere’s metal additive manufacturing process has transformed the manufacturing landscape by enabling the production of complex parts with unprecedented precision. Additive manufacturing has evolved from